This was a mock-up, that became a prototype, and then was put into use as test one. It needs to be rebuilt and refined, made lighter in weight, and adapted to other size rockets. I am repairing this model tonight for more flights Sunday. I am going to put it on a 6 liter rocket to see if it works up high as well as it did at 250 ft. or so. The Fritos can is just a holder. 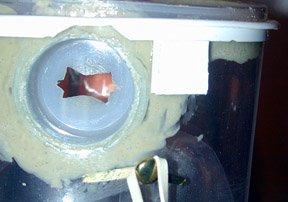
This is the keyhole. The shape of it will control when the system activates. It is a Fuji 35mm film can, cut down and PLP glued in place. 1. Launch position 2. Activation at this angle. |  |
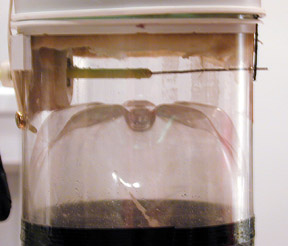
This pic shows the shaft, horizontal across the body. The lever and weight actuator are on the left, release pin and trigger on right. The shaft, crossbar and pin. The shaft is a piece of styrene, like a model parts "tree", the crossbar and pin are paper clip material. The 35mm film can lid locates the shaft and allows easy removal of the mechanism for adjusting. The spring acts to retract the shaft and pin. 3. Pin retracted, rubber band web pushing nosecone up. 4. Rubber band pulling nosecone off to one side, accordian folded trash bin liner parachute springing out. 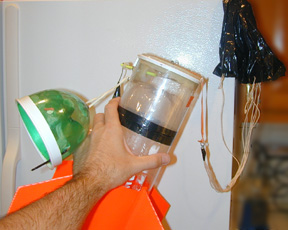
5. Deployment! |
|  |
This pic shows the weight and lever actuator. At launch this is vertical, as the rocket turns over (aided by the weight itself) the weight remains in place as the rocket body rotates around it. When the rocket reaches 35 to 40 degrees right or left of vertical, the shaft has rotated enough to retract. This is tunable by the sizing of the keyhole. 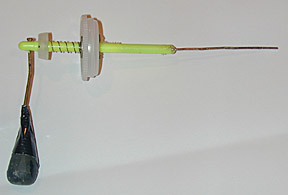
A view of, from left, the lever arm and weight, the spring retainer and spring, the 35mm lid, the crossbar, and the pin. This is in the retracted position, after apogee. In pictures 3 and 4 to the left, you can see the lips or flanges that allow the nose cone to be secure on the rocket at launch without danger of being jammed at apogee. The lower lip is the rim of a margarine tub, I got the idea for that from one of the Web Ring pages, the upper flange that mates with the lower one ifs cut from a 32 oz. "big gulp" type plastic cup the local convienence store had. Thanks to Bob "Rocket" Brown for noticing that it fit my guppy nosecone so nicely. Also visible is the Frito can lid that I glued in the top of the sleeve, just above the film can, to act as a bulkhead and parachute platform. The parachute is attached to this with a swivel. 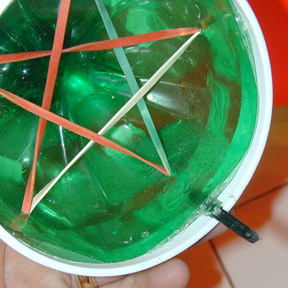 This pic shows the inside of the nosecone, the trigger, and the web of rubber bands. A couple of important points: The trigger is a piece of cable tie ground smooth on both sides. I put a liner sheet cut from a trash bin over the chute to keep it from getting caught in the web of bands. The white section fro mthe Big Gulp cup is very important, because when you cut the guppy nosecone from the 2 liter bottle, the edge of it is flimsy and will not locate on the rocket correctley. It also tends to pinch and create friction possibly preventing seperation. The relationship between the margarine tub lips and the big gulp rim is a nice "loosely tight" fit. |
|
|